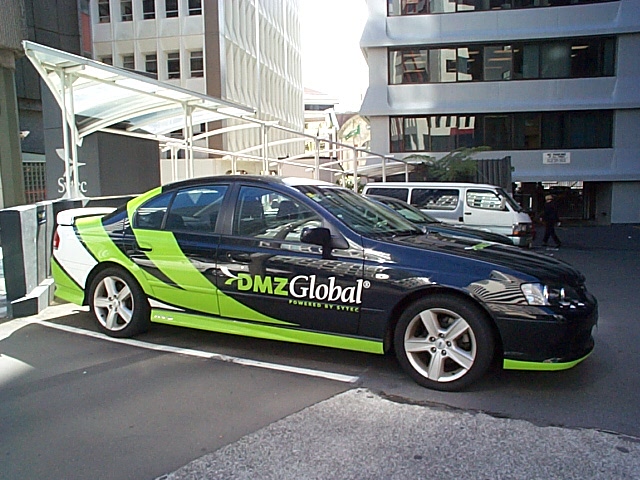
Cars have a finite lifespan, yet a breakthrough recycling technology pioneered by Eastman offers a solution to perpetually recycle certain automotive materials. Typically, when vehicles reach the end of their journey, their remains, known as automotive shredder residue (ASR) or "auto fluff," are disposed of in landfills or incinerated. Through collaborative efforts with various partners, Eastman has successfully demonstrated the molecular recycling of ASR.
Chris Scarazzo, Eastman's global automotive segment market manager, emphasizes the pivotal moment the automotive industry is facing globally, with a shift towards more sustainable practices. Molecular recycling presents a significant opportunity in this transition. The partnership between Eastman, the United States Automotive Partnership LLC (USAMP), PADNOS, a prominent mechanical recycling company, and Yanfeng, a global automotive parts supplier, showcased the feasibility of a closed-loop solution for automotive plastic waste in a 2021 study.
While originating from a U.S. study, the implications of this project reverberate globally, especially with evolving regulations. For instance, the European Commission is considering repealing Directive 2000/53/EC on end-of-life vehicles (ELV) in favor of new requirements aimed at reducing ELV waste. These new directives include targets for increasing the use of recycled content in automotive plastics.
Plastics are integral to modern automobiles, but their disposal poses challenges at the end of the vehicle's life cycle. ASR, comprising plastics, textiles/fibers, and other materials, accounts for a significant portion of automotive waste that historically couldn't be recycled conventionally, leading to landfilling or incineration. However, the industry recognizes the importance of finding alternatives to mitigate environmental impact, especially with regards to reducing greenhouse gas emissions and carbon footprints. Lightweight materials not only enhance fuel economy but are crucial in offsetting the weight of electric vehicle batteries.
“Modern cars are made with approximately 50% plastic by volume, on average, and this number is expected to increase as automotive manufacturers continue to seek lighter electric vehicles,” said Steve Crawford, Eastman’s executive vice president, manufacturing and chief sustainability officer.
“We’re demonstrating a future where automotive hard-to-recycle plastics and fibers are diverted from landfills and recycled to produce new automotive parts.”
Molecular recycling stands as the key to achieving circularity in recycling practices. Eastman's cutting-edge molecular recycling technologies have the potential to transform recycling by effectively processing challenging plastics, including those found in ASR. These innovative technologies deconstruct plastic waste at the molecular level, enabling the creation of recycled materials that are virtually identical to virgin materials in terms of performance and safety.
Among Eastman's breakthrough technologies is carbon renewal technology (CRT), capable of recycling a wide array of plastics. This technology was instrumental in demonstrating closed-loop recycling for ASR. In collaboration with PADNOS, Eastman utilized ASR as feedstock for its recycling process. Through CRT, Eastman transformed ASR into materials utilized in the production of new plastic resins. These resins were then molded by Yanfeng into automotive parts meeting stringent requirements set by major OEMs including Ford, GM, and Stellantis, all part of USAMP.
The outcomes of this endeavor exemplify the potential of collaborative efforts in fostering a sustainable future. Both mechanical recycling and molecular recycling play crucial roles and must complement each other to establish a robust recycling infrastructure suitable for modern needs.
“The collaboration on this project is indicative of the work that is needed to create closed-loop and circular-economy solutions,” said Kari Bliss, principal of sustainability at PADNOS. “Our purpose statement is on full display with this project — to continue to find ways to innovate, lead and make a positive impact in this world. We are proud to be the mechanical recycler involved in this complex endeavor, which is the first of its kind in North America.”
Chris Scarazzo, Eastman's global automotive segment market manager, emphasizes the pivotal moment the automotive industry is facing globally, with a shift towards more sustainable practices. Molecular recycling presents a significant opportunity in this transition. The partnership between Eastman, the United States Automotive Partnership LLC (USAMP), PADNOS, a prominent mechanical recycling company, and Yanfeng, a global automotive parts supplier, showcased the feasibility of a closed-loop solution for automotive plastic waste in a 2021 study.
While originating from a U.S. study, the implications of this project reverberate globally, especially with evolving regulations. For instance, the European Commission is considering repealing Directive 2000/53/EC on end-of-life vehicles (ELV) in favor of new requirements aimed at reducing ELV waste. These new directives include targets for increasing the use of recycled content in automotive plastics.
Plastics are integral to modern automobiles, but their disposal poses challenges at the end of the vehicle's life cycle. ASR, comprising plastics, textiles/fibers, and other materials, accounts for a significant portion of automotive waste that historically couldn't be recycled conventionally, leading to landfilling or incineration. However, the industry recognizes the importance of finding alternatives to mitigate environmental impact, especially with regards to reducing greenhouse gas emissions and carbon footprints. Lightweight materials not only enhance fuel economy but are crucial in offsetting the weight of electric vehicle batteries.
“Modern cars are made with approximately 50% plastic by volume, on average, and this number is expected to increase as automotive manufacturers continue to seek lighter electric vehicles,” said Steve Crawford, Eastman’s executive vice president, manufacturing and chief sustainability officer.
“We’re demonstrating a future where automotive hard-to-recycle plastics and fibers are diverted from landfills and recycled to produce new automotive parts.”
Molecular recycling stands as the key to achieving circularity in recycling practices. Eastman's cutting-edge molecular recycling technologies have the potential to transform recycling by effectively processing challenging plastics, including those found in ASR. These innovative technologies deconstruct plastic waste at the molecular level, enabling the creation of recycled materials that are virtually identical to virgin materials in terms of performance and safety.
Among Eastman's breakthrough technologies is carbon renewal technology (CRT), capable of recycling a wide array of plastics. This technology was instrumental in demonstrating closed-loop recycling for ASR. In collaboration with PADNOS, Eastman utilized ASR as feedstock for its recycling process. Through CRT, Eastman transformed ASR into materials utilized in the production of new plastic resins. These resins were then molded by Yanfeng into automotive parts meeting stringent requirements set by major OEMs including Ford, GM, and Stellantis, all part of USAMP.
The outcomes of this endeavor exemplify the potential of collaborative efforts in fostering a sustainable future. Both mechanical recycling and molecular recycling play crucial roles and must complement each other to establish a robust recycling infrastructure suitable for modern needs.
“The collaboration on this project is indicative of the work that is needed to create closed-loop and circular-economy solutions,” said Kari Bliss, principal of sustainability at PADNOS. “Our purpose statement is on full display with this project — to continue to find ways to innovate, lead and make a positive impact in this world. We are proud to be the mechanical recycler involved in this complex endeavor, which is the first of its kind in North America.”