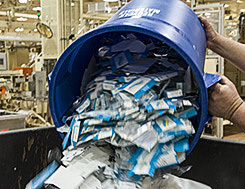
Dailycsr.com – 08 July 2015 – R.J Reynolds Tobacco Company has been active in the attempt of creating environment friendly sustainable future. Therefore its manufacturing branch “Tobaccoville” has initiated a “new recycling program” whereby all the waste paper produced at the “Making and Packing division” of the company everyday are being put into green use. Every bit of waste foil, cigarette, cardboard pieces, cartons, tipping papers, film, pack blamks and labels are gathered and sorted “for recycling”.
These waste materials are transported to another “recycling company” which segregates them further, puts them into bundles and sends then over to “a leading U.S. paper maker”, whereby these are transformed into “paper towels, toilet tissues, and napkins” among other commercial products.
Reynolds believes that “environmental sustainability” indicates “good business sense”, generating efficiency and cutting down on cost which has a cumulative value with every passing year. Whether, on a big or small scale, irrespective of its size, “environmentally sustainable practices” to continue:
“…to be a key element in RAI's transformation vision for leading change in the tobacco industry.”
The Tobaccoville’s sustainable recycling project had started “in July 2012”, which is run by the lead initiative of the employees. After a year of working the manufacturing team of R.J Reynolds, working on project came up with a “cost-effective plan” and efficient method of managing the waste products due to the complexity involved in segregating the mixture of “papers and other materials”.
In the senior staff-engineer, Charles Brintle’s words:
"It's like turning an aircraft carrier. It takes time to come up with a functional plan, and to get everyone trained on their role in the execution of it."
The process incorporated six team members from every shift of “Making and Packing” floor, who are termed as “recycling champions” who divided the task between themselves and in three days time they had trained “more than 800 employees”. In fact, all “contractor partners” had to compulsorily under-go these training sessions.
All had to be knowledgeable about which materials are to go for recycle and which “couldn’t”, whereby they were also instructed to make sure that every category of waste papers were kept in its right bins. As the practice turned into a habit, and by the end of December, the company had recycled “about 460 tons” papers, the employees were able notice that the rate of the “trash cans” filling up to the brim had slowed down consistently.
The senior area manager at Tobaccoville, Yong Yi talked about the recycling programme being a “good business decision”, whereby she said:
"This was one of our biggest landfilled waste streams. This brings in revenue and saves on landfill costs".
The major bulk of the waste produced at R.J. Reynolds is now being recycled after implementing the said recycling programme. In fact, the said practice generated a revenue of “$561,000” in the year of 2012 within the first six months.
References:
http://www.reynoldsamerican.com/environmental.cfm?plank=EnvironmentalSustainability1
These waste materials are transported to another “recycling company” which segregates them further, puts them into bundles and sends then over to “a leading U.S. paper maker”, whereby these are transformed into “paper towels, toilet tissues, and napkins” among other commercial products.
Reynolds believes that “environmental sustainability” indicates “good business sense”, generating efficiency and cutting down on cost which has a cumulative value with every passing year. Whether, on a big or small scale, irrespective of its size, “environmentally sustainable practices” to continue:
“…to be a key element in RAI's transformation vision for leading change in the tobacco industry.”
The Tobaccoville’s sustainable recycling project had started “in July 2012”, which is run by the lead initiative of the employees. After a year of working the manufacturing team of R.J Reynolds, working on project came up with a “cost-effective plan” and efficient method of managing the waste products due to the complexity involved in segregating the mixture of “papers and other materials”.
In the senior staff-engineer, Charles Brintle’s words:
"It's like turning an aircraft carrier. It takes time to come up with a functional plan, and to get everyone trained on their role in the execution of it."
The process incorporated six team members from every shift of “Making and Packing” floor, who are termed as “recycling champions” who divided the task between themselves and in three days time they had trained “more than 800 employees”. In fact, all “contractor partners” had to compulsorily under-go these training sessions.
All had to be knowledgeable about which materials are to go for recycle and which “couldn’t”, whereby they were also instructed to make sure that every category of waste papers were kept in its right bins. As the practice turned into a habit, and by the end of December, the company had recycled “about 460 tons” papers, the employees were able notice that the rate of the “trash cans” filling up to the brim had slowed down consistently.
The senior area manager at Tobaccoville, Yong Yi talked about the recycling programme being a “good business decision”, whereby she said:
"This was one of our biggest landfilled waste streams. This brings in revenue and saves on landfill costs".
The major bulk of the waste produced at R.J. Reynolds is now being recycled after implementing the said recycling programme. In fact, the said practice generated a revenue of “$561,000” in the year of 2012 within the first six months.
References:
http://www.reynoldsamerican.com/environmental.cfm?plank=EnvironmentalSustainability1